What Is Engine Vibration?
Engine vibration refers to unwanted oscillations and movements within an engine's rotating assembly. These vibrations are more than just uncomfortable—they can rob horsepower, accelerate wear, and even lead to catastrophic engine failure. Identifying and controlling engine vibration is essential for performance, efficiency, and reliability. There are three major types of engine vibration:- Lateral Vibration: Caused by uneven weight distribution in rotating parts like the crankshaft and pistons. It’s typically felt as a consistent thumping noise or sensation.
- Axial Vibration: Involves forward and backward motion of the crankshaft. It’s managed by thrust bearings and main bearing caps.
- Torsional Vibration: The most destructive type, caused by twisting and rebounding of the crankshaft due to the combustion pressure of each cylinder firing.
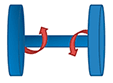
Torsional Vibration: The Hidden Engine Killer
While lateral and axial vibrations can be controlled mechanically, torsional vibration is more complex. It occurs when combustion events cause the crankshaft to twist and rebound rapidly. These rapid shifts in energy cause micro-movements that, if left unmanaged, result in long-term damage.How Torsional Vibration Works
The crankshaft in an internal combustion engine behaves like a torsional spring. When combustion fires, it sends a shockwave of force into the crank, causing it to flex and rebound. This movement is repeated hundreds of times per second, depending on engine RPM and cylinder count. For example, a 427ci V8 at 6,500 RPM with a 4th order torsional frequency vibrates at 433 Hz—meaning 433 twisting motions occur every second. That’s just one order; multiple orders can happen simultaneously, further complicating things.The Role of Amplitude and Resonance
Amplitude refers to the degree of crankshaft twist in response to torsional forces. At high RPM, this could mean 0.015 inches of movement. When vibration frequency aligns with the engine's natural resonance, amplitude spikes, sometimes doubling or tripling. This is when major failures occur—crankshaft snouts break, oil pumps wear prematurely, and timing misfires happen.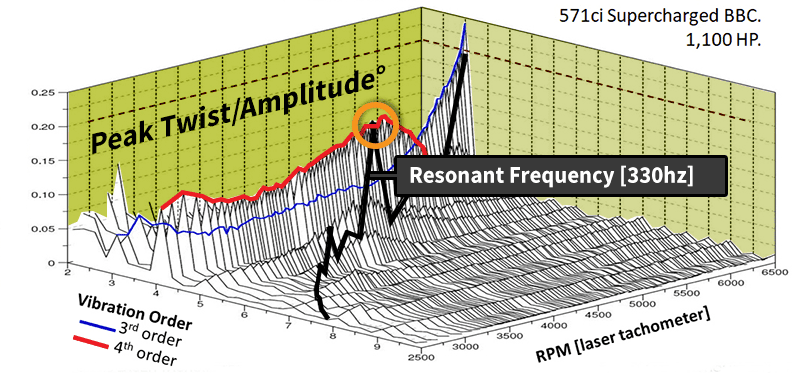
How Engine Vibration Is Measured
Engine vibration is measured using sensors and analyzers like Fast Fourier Transform (FFT) devices. These high-end tools capture vibration orders, frequencies, and amplitudes across the RPM range. This data is used by NVH (Noise, Vibration, Harshness) engineers to design appropriate dampers.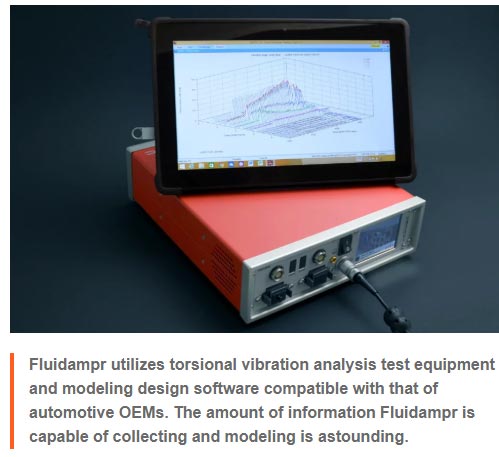
How Modifications Affect Engine Vibration
Engine mods such as forced induction, lightweight components, or increased rev limits change the vibration dynamics. More torque increases combustion pressure, which boosts vibration amplitude. Lighter parts shift the resonance frequency—often into dangerous RPM zones. When this happens, OEM harmonic balancers—typically tuned for narrow RPM ranges—can’t cope. Their rubber elastomer layers may crack, bulge, or fail. This is a major red flag. Additionally, using lightweight pulleys or deleting dampers entirely is risky. These components lack the inertia to absorb torsional forces, putting your entire engine at risk.Types of Harmonic Balancers
Also known as dampers or vibration absorbers, harmonic balancers come in various designs. Their purpose is to reduce or damp torsional vibration and protect your engine.- OEM Narrow-Range Balancers These are tuned to manage torsional vibration at a specific RPM—typically at cruising speed. They're cost-effective but ineffective once the engine is modified.
- Aftermarket Tuned Dampers These may offer modest improvements, but they're still limited in range. If your engine’s vibration signature changes, their effectiveness diminishes.
- Broad-Range Dampers (Like Fluidampr) These dampers use viscous fluid technology to absorb vibrations across the entire RPM range. They're ideal for performance builds and race applications. Fluidampr products are also SFI 18.1 certified for safety in motorsports.
Internal vs External Balance
Understanding your engine’s balance type is critical when selecting a damper:- Internal Balance: Crankshaft reciprocating counterweights are all within the crankshaft. Most modern engines use this design.
- External Balance: Crankshaft reciprocating counterweights are added to the damper or flywheel. Common in older or large-displacement engines like the Ford Windsor or Chevy 454.
External balance example. Note the crankshaft counterweight included on the hub.
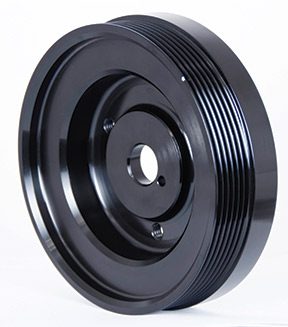
Internal balance harmonic damper example. Note the symmetry.
How Fluidampr Works
Fluidampr is a viscous harmonic damper that absorbs engine vibration through a unique three-part design:- Outer Housing: Mounts to the crankshaft and moves with it.
- Inner Inertia Ring: Free-floating and reacts to vibration events.
- Silicone Fluid: Provides resistance through shear and dissipates energy as heat.
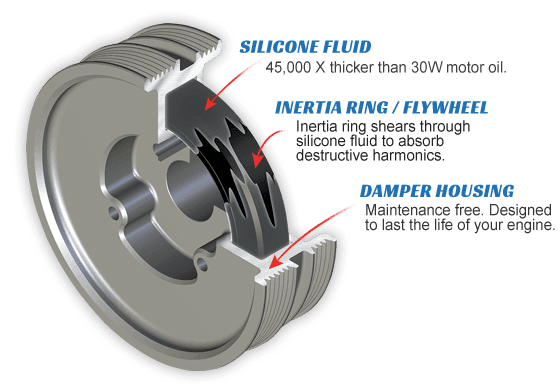
Why Silicone?
Silicone maintains consistent damping from -40°F to 300°F, dissipates heat efficiently, and offers low friction. It’s the ideal medium for torsional vibration control.Benefits of a Fluidampr Performance Damper
- Protects critical engine components from vibration-induced wear
- Improves horsepower and torque by increasing efficiency
- Enhances valve timing accuracy
- Supports the performance of other upgrades
- Complies with motorsports safety standards
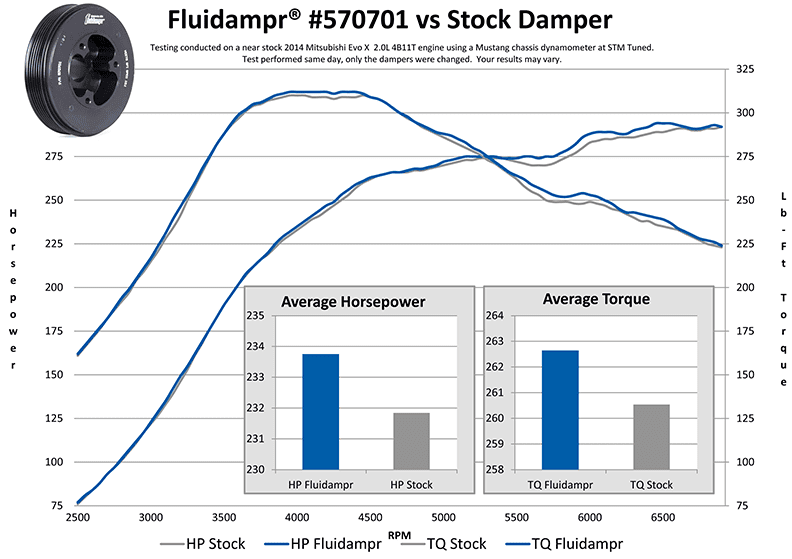
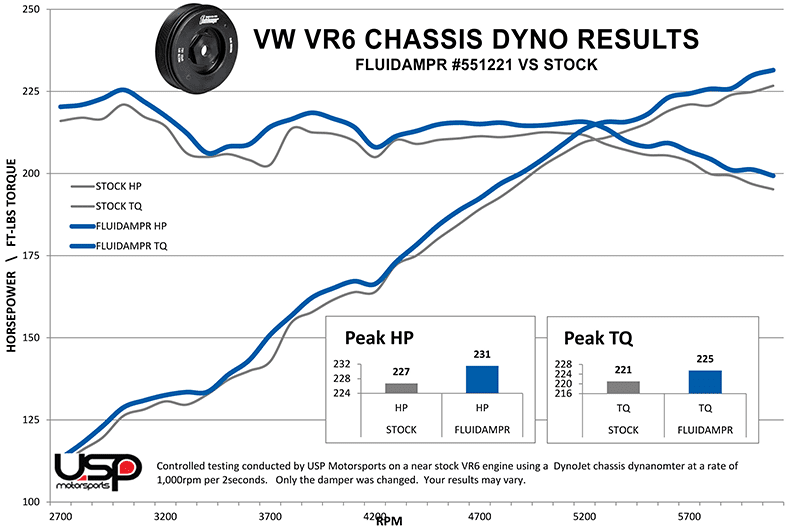
“Fluidampr proved to be the best. On top of the numerical data, there was a noticeable reduction in harmonics that could be felt in the concrete floor of the dyno cell.” — Jeremy Wagler, Engine Builder of the Year
When Should You Upgrade Your Harmonic Balancer?
It’s time to upgrade if:- You’ve added power (boost, cams, heads, exhaust).
- You’ve raised your engine’s redline.
- You’ve changed components of the rotating assembly (lightweight flywheel, pistons, rods).
- Your damper shows signs of wear.